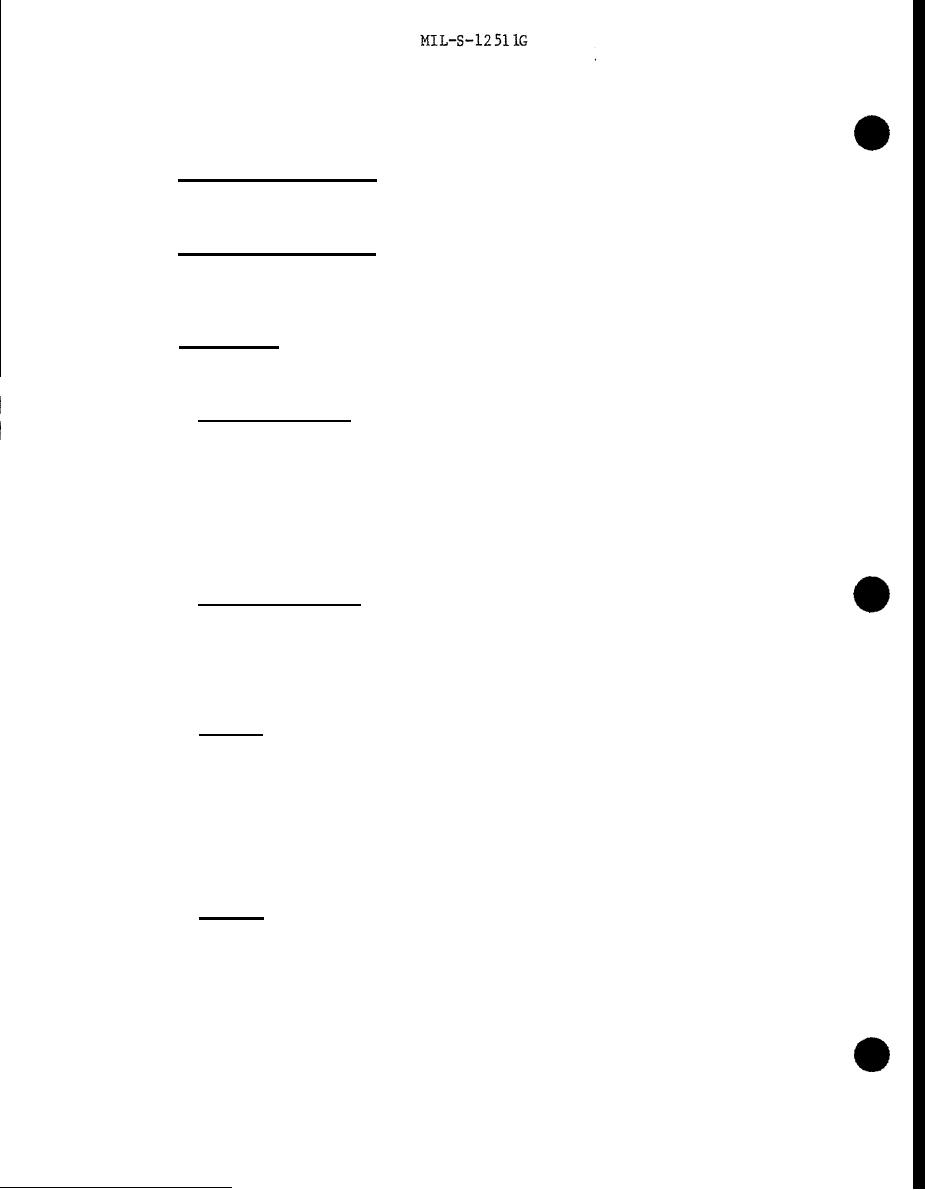
MIL-G-3859 with a 10-inch flexible extension. Accessibility to fittings shall
be provided without the removal or adjustment of accessories or parts. Panels
and plates equipped with hand-operable, quick-disconnect fasteners may be
removed to provide accessibility.
3.14 Treatment and painting. The portions of the sprayer normally painted
shall be cleaned, treated, and painted in" accordance with MIL-T-704, Type A,
color as specified (see 6.2).
3.15 Identification marking. The sprayer shall be identified in accordance
with MIL-STD-130. The marking shall be applied to the sprayer on plates
conforming to MIL-P-514, Type 1, Style 1, Composition C, of Type I, Grade A,
Class 1 material, 0.020 inch thick.
3.16 Workmanship. The sprayer shall be clean and free from sand, dirt, fins,
pits, scale, rust, burrs, sharp edges, cracks, poor or unsound welds, or any
other defect that could impair its performance or serviceability.
I
3.16.1 Metal fabrication. Metal used in fabrication shall be free from kinks
and sharp bends. The straightening of material shall be done by methods that
will not cause injury to the material. Corners shall be square and true. Flame
cutting, using tips suitable for the thickness of the steel may be employed
instead of shearing and sawing. All bends shall be made with controlled means
to insure uniformity of size and shape. Precaution shall be taken to avoid
overheating. Heated steel shall be allowed to cool slowly. External surfaces
shall be free of burrs, sharp edges and corners, except when sharp edges or
corners are required or where they are not detrimental to safety.
3.16.2 Bolted connections. Boltholes shall be accurately formed and shall
have the burrs removed. Washers or lockwashers shall be provided where
necessary. Matching thread areas securing bolts conforming to SAE J429 or cap-
screws shall be of sufficient strength to withstand the tensile strength of the
bolt. All fasteners shall be correctly torqued and shall have full thread
engagement. Bolts shall protrude not more than 2 full threads.
3.16.3 Welding. The surfaces of parts to be welded shall be free from rust,
scale, paint, grease, mill scale that can be removed by chipping and wire
brushing, and other foreign matter. Parent materials, weld filler metals, and
fabrication techniques shall be as required to enable the sprayer to conform to
the examination and test requirements specified in Section 4. Parts to be
joined by fillet welds shall be brought into as close contact as possible and in
no event shall be separated by more than 3/4 inch unless appropriate bridging
techniques are used. Unless otherwise specified (see 6.2), the welding process
used in fabrication of the sprayer shall be at the option of the contractor.
3.16.4 Welders. Before assigning any welder to manual welding work covered
by this specification, the contractor shall provide the contracting officer with
certification that the welder has passed qualification tests as prescribed by
either of the following listed codes for the type of welding operations to be
performed and that such qualification is effective as defined by the particular
code:
6
For Parts Inquires call Parts Hangar, Inc (727) 493-0744
© Copyright 2015 Integrated Publishing, Inc.
A Service Disabled Veteran Owned Small Business